青岛开投集团捷能汽轮机公司:数字化赋能工艺创新,跑出降本增效“加速度”
2025-04-24
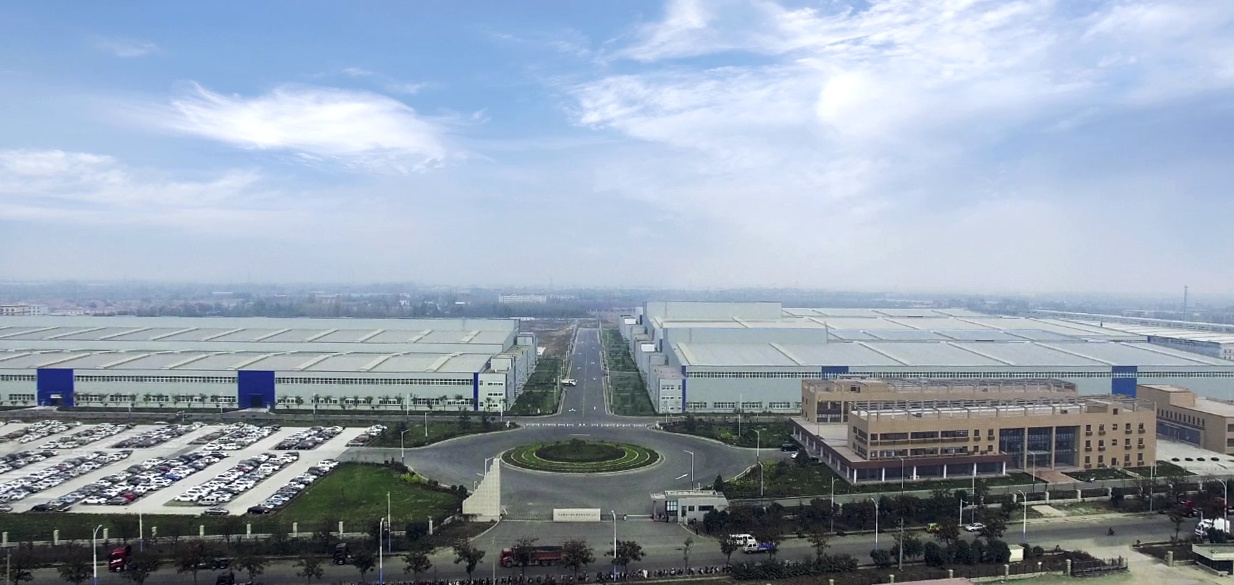
在推进企业高质量发展的征程中,青岛开投集团捷能汽轮机公司以数字化为核心驱动力,深度融入工艺创新,全面开启降本增效新篇章。公司工艺部门牵头成立降本增效攻关小组,通过跨部门、全流程协同,搭建起覆盖工艺设计、生产制造、库存管理等环节的信息化体系,探索出一条数字化转型与成本优化并行的创新发展路径。
构建工艺工装数字化体系,从源头控成本
公司着力打造工艺工装数字化体系,筑牢降本增效根基。一方面,建立汽轮机产品成本核算基础数据库,完善基型产品数据,大幅提升报价精准度;另一方面,运用ERP系统实现设计数据与分厂上报数据的数字化比对,严格审核确保工时合理。同时,推进工装与工艺流程参数化、数字化设计,构建工装通用化设计体系。以隔板焊接胎具为例,实施数字化管理后,6套胎体直接节约成本7万元,充分展现出数字化在源头降本上的显著成效。
深化工艺创新与数字化融合,向技术要效益
公司将工艺创新与数字化深度融合,持续挖掘降本潜力。通过建立三维叶片开发数字化仿真编程体系,成功实现叶片自制加工,有效降低生产成本。目前,已构建汽轮机三维叶片数字化、参数化模块,完成18种叶片的自制开发。此外,创新改进叶片毛坯加工方式,将锻造改为圆柱料线切割,累计节约成本约32万元。针对第五代汽轮机动静叶片、整体转子等关键部件,工艺部门提前运用数字化仿真模型开展自制工艺研究。若选择外协加工,预估费用高达200万元,通过自主试制成功后,可降低制造成本约60万元,有力突破技术瓶颈与成本困局。
推动生产库存数据联动,全链条降成本
公司强化生产与库存数据联动管理,实现全链条成本优化。通过实施叶片库存数字化联动管理,改制库存转动环、汽缸水试闷板等工装,自去年以来已消化库存价值近15万元。在刀具消耗管理上,大力推动分厂采用国产刀具替代进口刀具,预计年度可节省成本约34万元,切实将数据价值转化为降本实效。
下一步,青岛开投集团捷能汽轮机公司将锚定数字化转型方向,重点推进钢板数字化采购、刀具数字化直采、枞树形刀具重新刃磨等工作。通过强化数字化赋能、深化部门协同、增强全员降本意识,持续推动降本增效工作向纵深发展,为企业高质量发展注入更强动能。